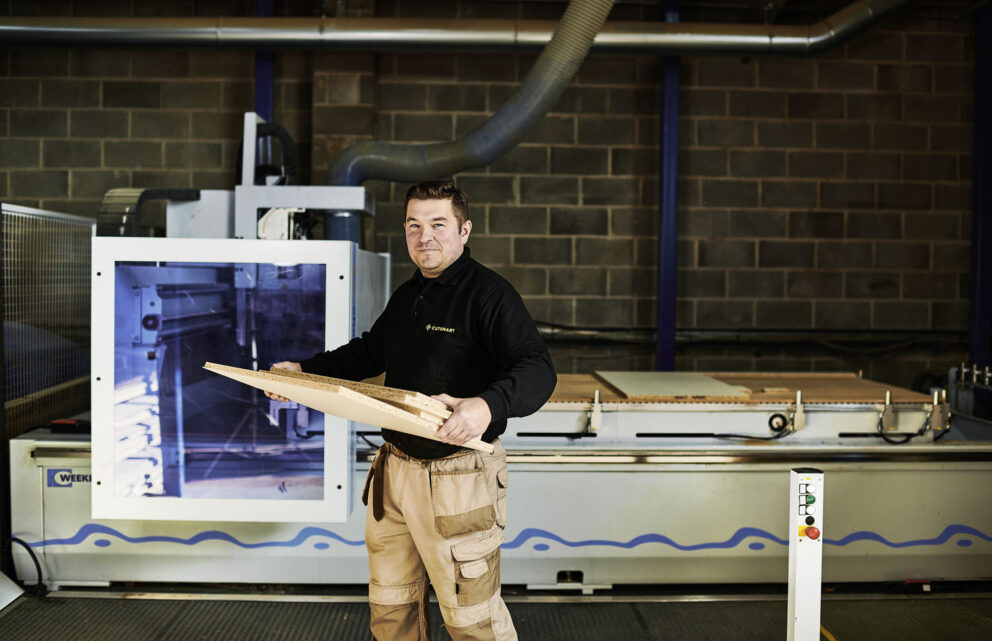
MDF vs Plywood: Which Should You Choose for Your Next Project?
Understanding Plywood and MDF
When it comes to choosing materials for various projects, two popular options that often come into consideration are Plywood and Medium-Density Fibreboard (MDF). Plywood is a versatile engineered wood product made by glueing together several layers of thin wood veneers, creating a strong and durable sheet. It is commonly used in furniture construction, cabinetry, flooring, and even structural applications.
On the other hand, MDF is a composite wood product made from wood fibres and resin binders, resulting in a smooth and consistent panel. MDF finds its applications in interior panelling, furniture manufacturing, moulding, and more. Understanding the differences between plywood and MDF is crucial as it allows us to make informed decisions and choose the most suitable material for specific projects.
Factors such as strength, moisture resistance, cost, and finishing options vary between the two, making it essential to assess their characteristics carefully before embarking on any construction or design endeavour.
Examining the Construction of Plywood and MDF
Plywood and Medium-Density Fibreboard (MDF) differ in their composition, leading to variations in their properties and performance. Plywood is crafted by layering multiple thin wood veneers, usually of hardwood or softwood, and bonding them together with adhesives. This construction creates a panel with alternating grain directions in each layer, providing strength and stability. The arrangement of the layers, known as plies, contributes to plywood's ability to resist warping and splitting.
On the other hand, MDF is made by breaking down wood fibres into small particles and combining them with resin binders. This mixture is then subjected to high pressure and heat, resulting in a dense and uniform panel. The absence of distinct wood grains in MDF allows for a smoother surface and consistent strength throughout the material. The composition of plywood and MDF plays a crucial role in determining their structural integrity, workability, and suitability for specific applications.
Strength and Durability of MDF vs Plywood
When it comes to strength and durability, plywood and Medium-Density Fibreboard (MDF) exhibit distinct characteristics. Plywood, with its layered construction, offers notable strength and resilience. The arrangement of multiple wood veneer layers creates a cross-grain pattern, enhancing its structural integrity. This design disperses stress and prevents the propagation of cracks, making plywood highly resistant to warping and splitting. Additionally, the use of high-quality adhesives in plywood manufacturing ensures strong bonding between layers, further enhancing its durability.
In contrast, MDF possesses a different kind of strength. Despite being denser than plywood, MDF is inherently less prone to warping, splitting, and cracking due to its uniform composition and lack of natural wood grains. The homogeneous distribution of wood fibres and resin binders throughout the panel contributes to its overall strength.
However, it is worth noting that MDF is more susceptible to moisture damage compared to plywood, making proper sealing and protection essential. Ultimately, the choice between plywood and MDF in terms of strength and durability depends on the specific requirements of the project, the anticipated load-bearing capacity, and the environmental conditions in which the material will be used.
Moisture Resistance: Plywood vs MDF
Moisture resistance is an important factor to consider when choosing between plywood and Medium-Density Fibreboard (MDF) for various applications. Plywood, particularly when utilising exterior-grade or marine-grade options, offers commendable resistance to moisture. The adhesive used in its construction, combined with the natural water repellency of certain wood species, makes plywood resistant to warping, swelling, and delamination when exposed to moisture or high humidity. This makes it a preferred choice for outdoor projects or areas prone to moisture, such as bathrooms or kitchens.
On the other hand, MDF has lower inherent moisture resistance. It is more susceptible to swelling, warping, and damage when exposed to moisture, as its composition primarily consists of wood fibres and resin binders. To mitigate this, proper sealing, such as priming and painting with water-resistant coatings, is crucial when using MDF in areas where moisture exposure is likely. It's important to note that even with proper sealing, MDF may not perform as well as plywood in consistently wet or high-moisture environments.
Understanding the moisture resistance properties of plywood and MDF is essential in selecting the appropriate material to ensure the longevity and performance of projects in various conditions.
MDF vs Plywood: Which Is More Budget-Friendly?
When it comes to budget considerations, plywood and Medium-Density Fibreboard (MDF) have different cost factors to take into account. Plywood typically has a wider range of pricing options, depending on factors such as the wood species used, the grade of plywood (interior, exterior, or marine), and the thickness of the panels. Generally, plywood tends to be more expensive than MDF due to the manufacturing process and the use of real wood veneers. On the other hand, MDF is often more budget-friendly, as it is made from wood fibres and resin binders, which are less costly compared to natural wood veneers. MDF is also more readily available and typically sold at a lower price per sheet compared to plywood. However, it's important to consider specific applications when evaluating cost considerations.
Plywood's strength and durability may make it a cost-effective choice for projects where longevity and structural integrity are paramount, such as furniture construction or load-bearing applications. Meanwhile, MDF's affordability and smooth surface make it a cost-effective option for interior panelling, decorative elements, or non-structural applications. Ultimately, the cost-effectiveness of plywood or MDF depends on the specific requirements, project size, and available budget, making it crucial to assess the trade-offs between cost and desired outcomes when making a decision.
Applications and Uses of MDF & Plywood
Plywood and Medium-Density Fibreboard (MDF) have distinct applications and excel in different areas of construction and design. Plywood is widely used in various industries due to its strength, versatility, and durability. It finds extensive applications in furniture manufacturing, where it provides a sturdy base for tables, chairs, and cabinets. Additionally, plywood is favoured for cabinetry, offering stability and resistance to warping. In the construction industry, plywood serves as a reliable material for structural elements like walls, floors, and roofs. Its strength and dimensional stability make it a go-to choice in demanding projects. On the other hand, MDF is highly valued for its smooth and consistent surface, making it ideal for interior panelling applications. It can be easily shaped, allowing for intricate designs in furniture construction, such as curved or ornate details. MDF is also commonly used for moulding, as its uniform composition allows for precise and clean cuts.
The versatility of MDF makes it suitable for projects that prioritise design aesthetics and where weight is not a significant factor. Overall, plywood shines in applications that require strength and durability, while MDF excels in projects that emphasise design flexibility and a smooth surface finish.
Finishing Options: Surface Treatments for Plywood and MDF
Both plywood and Medium-Density Fibreboard (MDF) offer a range of finishing options to enhance their appearance and protect their surfaces. Plywood provides excellent versatility when it comes to finishing. It readily accepts various treatments such as staining, painting, and veneering. Staining allows the natural grain of the wood veneer to shine through, creating a warm and rich look.
Painting provides endless colour options, allowing for customisation and creativity in design. Veneering involves applying a thin layer of real wood veneer to the surface, offering the aesthetics of solid wood while benefiting from plywood's structural properties. On the other hand, finishing MDF presents some challenges and benefits. MDF has a smooth and uniform surface, making it ideal for achieving a flawless painted finish. However, due to its composition, MDF is highly absorbent and prone to swelling when exposed to moisture. Therefore, proper priming is essential to seal the surface before painting. Edge sealing is also crucial to prevent moisture penetration and maintain the integrity of the material. Despite these considerations, the smooth surface of MDF allows for a seamless and professional-looking paint finish. It's worth noting that MDF does not have a natural grain pattern, limiting the options for staining or veneering.
Understanding the surface treatment options and considerations for both plywood and MDF helps in selecting the appropriate finishing techniques to achieve the desired aesthetic results while ensuring the durability and longevity of the finished product.
Environmental Impact: Sustainability Factors to Consider
Considering the environmental impact of materials is crucial in today's environmentally conscious world. Plywood and Medium-Density Fiberboard (MDF) production have varying sustainability factors to consider. Plywood, being made from wood veneers, relies on the responsible sourcing of timber. Sustainable plywood options are available, such as those certified by organisations like the Forest Stewardship Council (FSC), which ensure that the wood used comes from responsibly managed forests. FSC-certified plywood promotes biodiversity, protects indigenous communities, and mitigates deforestation. MDF, on the other hand, is made from wood fibres and resin binders.
The production process of MDF involves breaking down wood fibres and using synthetic binders, which can have environmental implications. However, efforts are being made to produce eco-friendly MDF, such as using formaldehyde-free resins or recycled wood fibres. Additionally, certifications like the Sustainable Forestry Initiative (SFI) and the Programme for the Endorsement of Forest Certification (PEFC) can ensure sustainable practices in MDF production. Exploring sustainable alternatives like bamboo-based plywood or fiberboard made from agricultural waste can also contribute to reducing environmental impact. When choosing between plywood and MDF, considering the environmental certifications, responsible sourcing, and sustainable alternatives can help minimise the ecological footprint of the chosen material and promote a more sustainable approach to construction and design.
Cutting and Shaping: Which Material Is Easier to Work With?
When it comes to cutting and shaping, both plywood and Medium-Density Fibreboard (MDF) offer unique characteristics and considerations. Plywood is generally easier to work with in terms of cutting and shaping, especially when using standard woodworking tools. It can be cut smoothly with a saw, whether it's a circular saw, jigsaw, or table saw. Plywood's layered construction provides stability and reduces the risk of tear-out or splintering. Additionally, it is relatively easy to create intricate shapes or curves with plywood due to its inherent flexibility. On the other hand, MDF presents its own challenges and advantages. MDF is denser and softer than plywood, making it easier to cut through with less effort. However, the fine wood fibers and resin binders in MDF can dull blades more quickly, requiring periodic sharpening or replacement of cutting tools.
Precision cuts in MDF are achievable with proper techniques, but extra care must be taken to prevent chipping or splintering along the edges. Despite these challenges, MDF's homogeneous composition allows for smooth, clean cuts, making it ideal for projects that require precision and a flawless finish. Ultimately, the choice between plywood and MDF for cutting and shaping depends on the specific requirements of the project, the desired level of precision, and the tools and techniques available to achieve the desired results.
Talk to Cutsmart about us cutting to size any of your board requirements.
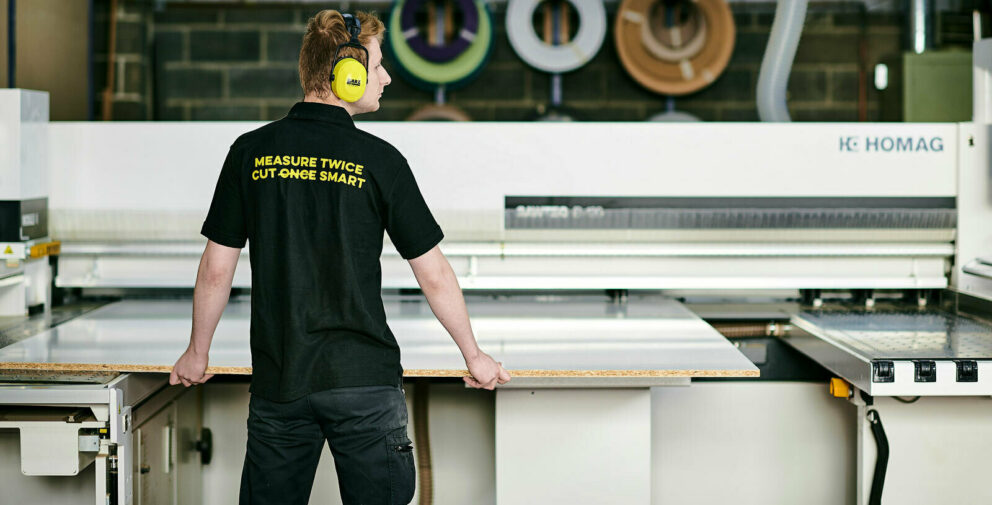
Stability and Warping: How Plywood and MDF React Over Time
Stability and resistance to warping are critical factors to consider when selecting materials for construction and design projects. Plywood, with its layered construction, offers inherent stability and exceptional resistance to warping. The alternating layers of wood veneers, each oriented in a different grain direction, create a balanced and reinforced structure. This cross-grain pattern helps distribute stress and minimises the likelihood of warping or twisting. The adhesive used in plywood production further enhances its stability by firmly bonding the layers together. This structural integrity allows plywood to maintain its shape and dimensional stability over time, making it a reliable choice for various applications.
In contrast, MDF demonstrates higher stability and is less prone to warping compared to natural wood. Its composition of wood fibres and resin binders provides a uniform density and consistency throughout the panel. Unlike solid wood, which can be affected by changes in moisture and temperature, MDF's homogeneous structure minimises the risk of warping or shrinking. This stability makes MDF a suitable material for projects that require precision and where dimensional changes could compromise the integrity of the design.
Both plywood and MDF offer advantages in terms of stability and resistance to warping. Plywood's layered construction provides inherent strength and stability, while MDF's uniform composition offers consistent performance over time. Understanding these characteristics helps in choosing the appropriate material based on the specific requirements and potential environmental conditions of the project.
Weight and Density: Comparing the Physical Characteristics of MDF & Plywood
Plywood and Medium-Density Fibreboard (MDF) exhibit differences in weight and density, influencing their suitability for various applications. Plywood tends to be lighter and less dense compared to MDF. This is due to the nature of its construction, which involves multiple layers of wood veneers. The use of lighter wood species or thinner veneers can further reduce its weight. The lower density of plywood can be advantageous in projects where weight is a concern, such as in furniture or interior panelling applications. It makes handling and installation easier, especially for larger pieces. On the other hand, MDF is denser and heavier due to its composition of wood fibres and resin binders. This density provides stability and a solid feel to MDF products. The weight and density of MDF make it well-suited for applications that require a substantial and durable material, such as cabinets, shelving, and structural components. Understanding the weight and density characteristics of plywood and MDF is crucial in selecting the appropriate material based on the specific project requirements, load-bearing considerations, and ease of handling.
Strength in Different Conditions: Plywood and MDF in Various Environments
The performance of plywood and Medium-Density Fibreboard (MDF) can vary in different environmental conditions, making it important to consider their suitability for specific applications. Plywood exhibits excellent strength and durability in various environments, including high humidity or temperature variations. Its layered construction and the use of exterior-grade or marine-grade options enhance its resistance to moisture and weathering. This makes plywood well-suited for outdoor applications such as construction projects, exterior cladding, or marine applications where exposure to moisture is a concern. Additionally, plywood's natural resistance to warping and dimensional stability allows it to maintain its strength and structural integrity in changing conditions.
On the other hand, MDF is more susceptible to moisture and temperature variations compared to plywood. It has a lower moisture resistance due to its composition of wood fibres and resin binders. While MDF can still perform adequately in controlled indoor environments, it requires proper sealing and protection to prevent swelling or damage from moisture exposure. This makes MDF more suitable for interior applications such as furniture, cabinetry, or decorative elements, where it can provide a smooth surface finish and design flexibility.
Considering the environmental conditions and specific requirements of a project is crucial when choosing between plywood and MDF. Plywood's strength and resistance to moisture make it a reliable choice for outdoor or high-humidity environments, while MDF excels in controlled indoor applications where proper sealing can be implemented. Understanding the strengths and limitations of each material ensures their optimal performance and longevity in various environmental conditions.
MDF or Plywood -Which Material Offers Better Sound Absorption?
When it comes to sound absorption, plywood and Medium-Density Fibreboard (MDF) exhibit different properties that can impact noise reduction and insulation in different settings. Plywood, with its layered construction and solid wood composition, offers inherent sound-dampening characteristics. The multiple layers of wood veneers and their ability to dissipate sound waves make plywood effective in reducing noise transmission. This makes it a suitable choice for applications where noise reduction is desired, such as in music studios, home theatres, or soundproofing partitions.
MDF, on the other hand, possesses denser and more uniform composition, which contributes to its superior sound absorption properties. The fine wood fibres and resin binders in MDF help to absorb and deaden sound, making it effective in reducing echo and minimising noise transmission. MDF panels with appropriate thickness and density can provide excellent sound insulation in applications like recording studios, acoustic panels, or interior walls where noise control is a priority.
Both plywood and MDF can contribute to noise reduction and insulation, but their specific properties lend themselves to different settings. Plywood's layered construction makes it suitable for reducing noise transmission, while MDF's dense composition offers superior sound absorption. Understanding these characteristics helps in selecting the appropriate material based on the desired level of sound reduction, the specific application, and the acoustic requirements of the space.
Design Consideration - Plywood and MDF in Interior and Furniture Design
Both plywood and Medium-Density Fibreboard (MDF) offer unique design possibilities and considerations in interior and furniture design. Plywood, with its natural wood grain and layered construction, adds warmth and character to various design styles. It can be showcased as a prominent feature, highlighting the beauty of the wood veneers. Additionally, plywood's strength and stability allow for structurally sound furniture and architectural elements. Its versatility enables the creation of clean lines and modern aesthetics. Plywood can also be easily shaped and bent to achieve unique and sculptural forms, making it ideal for contemporary or avant-garde designs.
In contrast, MDF's smooth and consistent surface makes it highly suitable for achieving intricate designs and details. Its homogeneous composition allows for precise cutting and carving, enabling the creation of intricate patterns, mouldings, or decorative elements. MDF provides a flawless canvas for painting or veneering, allowing for customisation and a wide range of design possibilities. It excels in achieving a seamless and polished finish, making it a preferred choice for traditional or ornate styles. MDF's versatility lends itself well to both modern and classic design aesthetics.
When considering interior and furniture design, plywood offers the natural beauty of wood and structural strength, while MDF provides a smooth surface for intricate detailing and design customisation. Understanding the unique characteristics of each material helps designers and architects choose the most suitable option based on the desired style, functional requirements, and design vision.
Take a look at Cutsmart's extensive range of boards for all of your interior requirements
Maintenance and Care - Caring for Plywood and MDF Products
Proper maintenance and care are essential for prolonging the lifespan and preserving the aesthetics of plywood and Medium-Density Fibreboard (MDF) products. When it comes to plywood, regular cleaning is key to keep it in good condition. Use a soft cloth or sponge dampened with mild soap and water to remove dust or dirt. Avoid using harsh chemicals or abrasive cleaners that can damage the surface. If scratches or dents occur, they can be repaired by lightly sanding the affected area and applying a matching wood finish or sealant. It's also important to periodically check for signs of moisture damage, especially in areas prone to humidity or moisture exposure. Applying a protective sealant or finish can help enhance plywood's resistance to moisture and maintain its appearance over time.
As for MDF, moisture protection is crucial to prevent swelling or warping. It's essential to avoid prolonged exposure to water or high humidity environments. In areas where moisture is a concern, such as bathrooms or kitchens, proper sealing or finishing is necessary to create a protective barrier against moisture absorption. When cleaning MDF, use a damp cloth or sponge with mild soap and water, being cautious not to oversaturate the surface.
Avoid using abrasive materials or strong solvents that can damage the finish or cause discolouration. Regularly inspect MDF for any signs of damage or wear, and promptly address any issues to prevent further deterioration.
By following these maintenance tips, both plywood and MDF products can maintain their appearance and structural integrity for years to come. Regular cleaning, proper sealing, and addressing potential issues in a timely manner contribute to the longevity and overall performance of these materials in various applications.